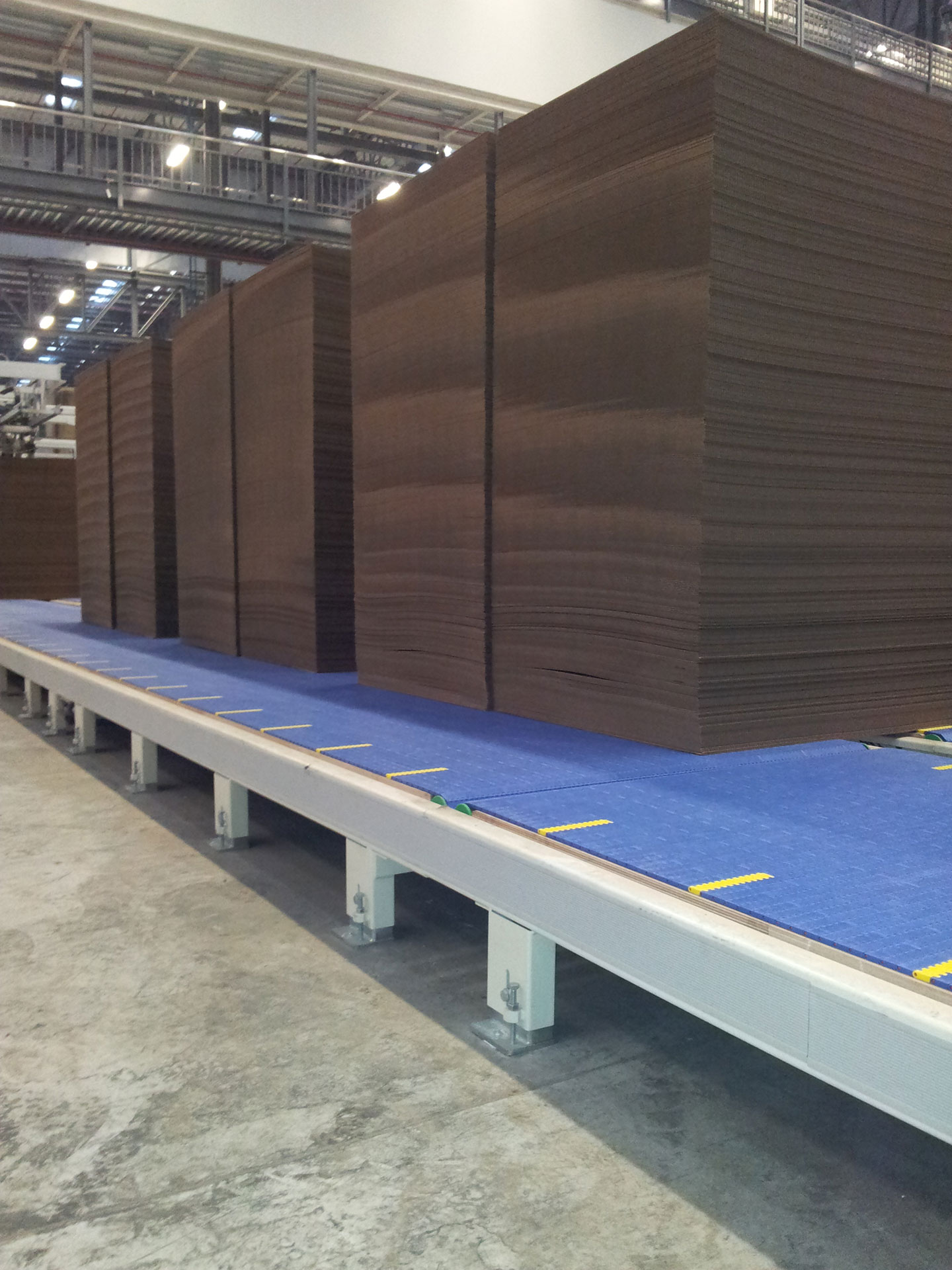
At Warak Group, thanks to the input of valued customers, we have just developed the concept H45 for all our intralogistics equipment.
In the corrugated factories, one of the biggest risks is the fire due to some electrical failure or mechanical friction. A fire in a corrugated factory develops extremely fast due to the dust of the whole environment and the paper and corrugated board around. We are used to live with that risk, and it is present on every factory but, there are some points where cleaning is not easy.
At Warak Group, we have designed the conveyor belt frames for the intralogistics equipment at an upgradable height of 450mm over the floor, 3 steps up. The main reason for that is to allow the use of automatic cleaning robots to go underneath our belts. The industrial “roombas” are coming!!
Not all belts in the market allow to do so. On the contrary, with most of them, that is not possible since are built with cheaper laser cut steel plates going down to the floor or using simple screws as legs to support them not higher than 350-380mm or the use of cable channels laying directly on the floor underneath the belts crossing everywhere.
The concept takes into consideration that actual height of 350mm already hurt our knees and the knees of employees if proper crossing paths are not provided. Higher path prevents to jump on the conveyors if there is no path or steps. On the other side, stack height of stacker and prefeeder can be easily regulated to 450mm not losing stack transport ability as we keep the 1800mm stack height over the factory up to the rack.
Integrated cable path into the belt steel-bent frames helps to free up all the floor underneath the conveyors. Like this there is no more pieces of board and dust accumulated underneath the belts, having a site that complies much more with BRC certification for the food industry and safety at work.