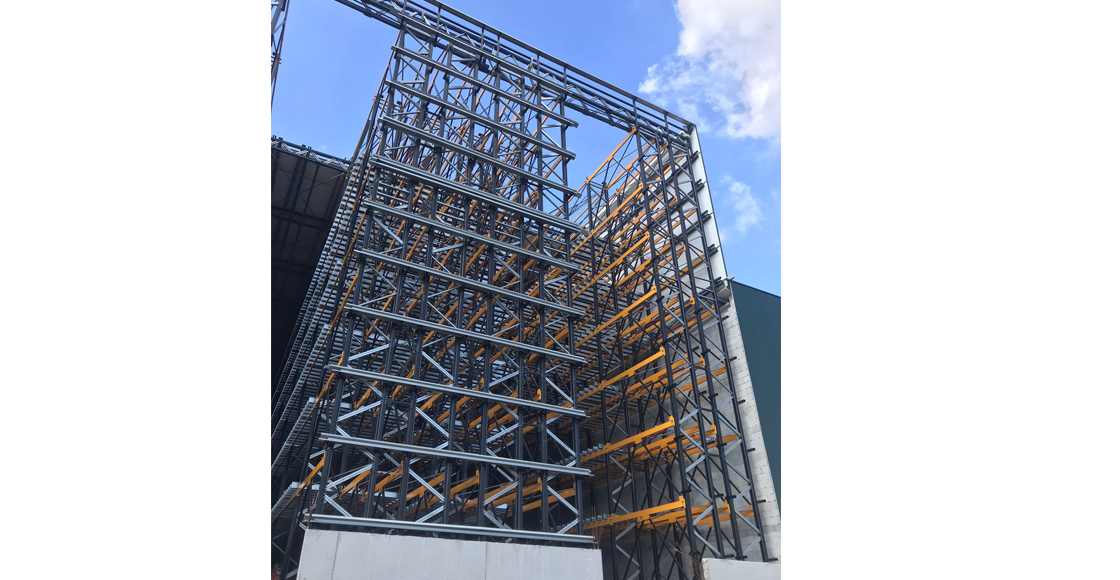
In an intermediate cardboard product warehouse, there are two variables that define it: the target storage capacity and the transfer capacity (or transport of square metres of cardboard per hour of work).
Contrary to what it may seem at first glance, the transfer capacity of cardboard per hour is much higher than any traditional conveyor or roller system. The main reason for this is that, at the corrugator exit, we create blocks which are groupings of stacks of cardboard across the width and also the length of the corrugator.
These super stacks of board, which can contain from 1,800m2 in double board to 4,500m2 in micro flute board, will travel from the corrugator to the warehouse and from there to the converting section. Once in the converting section, the stacks are separated and delivered to each machine.
In these 12 years of evolution of vertical warehouses, the cardboard sector has undergone major changes, one of the most obvious of which is the size of orders, which are becoming shorter and shorter. But less square meters per order means more transport of blocks, so how do you deal with the transport of smaller orders?
What about the factories in the Asian market that operate using this technology? As with all systems, when entering these markets we had to adapt to their needs. In this way, we went from loading one block to being able to load 2 or 4 different order blocks at the same time, reducing the number of cycles of the stacker cranes and maintaining the m2 transfer ratio that a high-capacity factory with short orders needs.
Listing the solution is simple, but the technology that works inside is much more complex. A technology that ranges from the specially designed loading stations to the programming of the intralogistics system and its stacker cranes. A challenge, which together with digital simulations, has allowed us to participate in new projects all over the world.